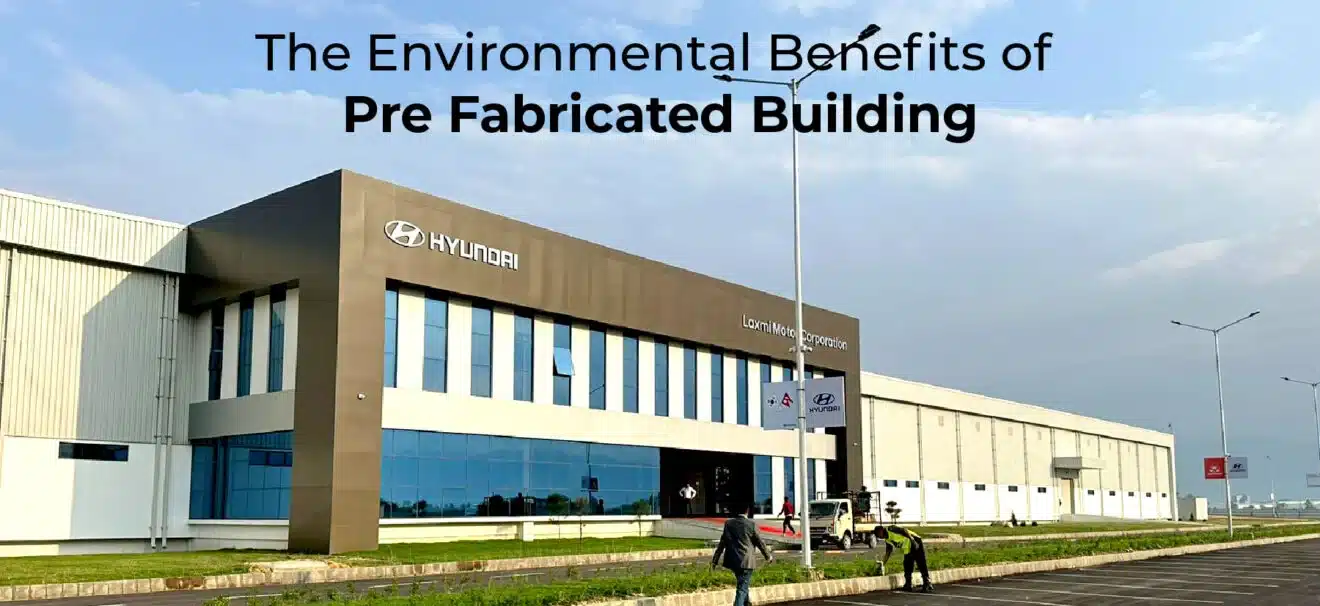
Nowadays the environmental consciousness is growing, and everyone is more focused on sustainability and the things that can not impact Global warming. Similarly, the construction industry is under increasing pressure to adopt sustainable practices. PEB buildings, often referred to as “prefabs,” have emerged as a promising solution that offers a multitude of environmental benefits.
Through this article we will learn about the ways in which prefabs contribute to a greener construction process, reducing waste, conserving energy, and minimizing environmental impact.
How PEB Benefits Environment?
1. Significant Reduction in Construction Waste
One of the most notable advantages of Prefeb construction is the substantial reduction in construction waste. Traditional construction sites are notorious for generating large amounts of waste, often ending up in landfills. Studies suggest that prefab construction can reduce construction waste by up to 90%. This reduction is achieved through precise manufacturing processes in controlled factory environments, where material usage is optimized, and excess materials can be reused or recycled.
2. Resource Efficiency and Conservation
Prefabs promote resource efficiency through the use of standardized components and modular design. By minimizing material variations and optimizing material usage, prefabs conserve valuable resources. Also, many prefab manufacturers incorporate recycled and sustainable materials into their designs, further reducing the demand for virgin resources. For instance, some prefabs utilize recycled steel, which consumes 74% less energy to produce than virgin steel.
3. Energy Efficiency and Reduced Carbon Footprint
PEB buildings are inherently more energy-efficient than their traditionally constructed counterparts. The controlled factory environment allows for precise insulation installation and airtight construction, minimizing energy loss. This translates to reduced heating and cooling costs for building occupants and a smaller carbon footprint. Prefab can be up to 30% more energy-efficient than traditional buildings. Furthermore, some prefabs are equipped with solar panels and other renewable energy sources, further reducing their reliance on fossil fuels.
4. Faster Construction Timelines and Reduced Disruption
PEB construction significantly accelerates construction timelines compared to traditional methods. Since components are manufactured off-site, construction can proceed concurrently with site preparation, reducing overall project duration by up to 50%. This not only saves time but also minimizes disruption to the surrounding environment, reducing noise pollution, dust, and traffic congestion associated with prolonged construction activities.
5. Adaptability and Reusability
PEB buildings are designed for adaptability and reusability. Many prefab components are modular and can be easily disassembled and reconfigured for different uses. This flexibility extends the lifespan of the building and reduces the need for demolition and reconstruction, which are resource-intensive processes. Some prefabs are even designed to be relocated entirely, further minimizing environmental impact.
6. Water Conservation
PEB construction often incorporates water-saving technologies, such as low-flow fixtures and rainwater harvesting systems. These features reduce water consumption during construction and throughout the building’s lifespan. Additionally, the controlled factory environment minimizes water waste during manufacturing processes.
Conclusion
Pre Fabricated Building, such as those offered by Willus Infra, represent a significant step towards a more sustainable construction industry. We reduced waste, resource efficiency, energy conservation, and adaptability contributing to a smaller environmental footprint. As technology advances and construction practices evolve, prefabs are likely to play an increasingly important role in building a greener future. At Willus Infra, we are committed to providing high-quality, sustainable pre engineered building solutions that benefit both our clients and the environment.
Frequently Asked Questions
1. How do PEB buildings from Willus Infra reduce construction waste?
At Willus Infra, our commitment to sustainability begins at the manufacturing stage. Our prefabricated buildings are designed to optimize material use and minimize waste through precise engineering and standardized components. We strive to reuse or recycle excess materials, significantly reducing the amount of waste sent to landfills compared to traditional construction.
2. Are PEB buildings energy efficient?
Yes, energy efficiency is a core principle in our prefab design. The controlled factory environment allows for precise installation of insulation and airtight construction, reducing energy loss and lowering heating and cooling costs for building occupants. Additionally, we offer options for integrating renewable energy sources like solar panels to further reduce energy consumption and carbon footprints.
3. How does Willus Infra’s PEB construction process reduce disruption to the environment?
Our off-site manufacturing process significantly shortens on-site construction time, minimizing disruption to the surrounding environment. This means less noise pollution, dust, and traffic congestion compared to traditional construction projects. By streamlining the construction process, we aim to create a more pleasant and sustainable experience for both our clients and the communities where we build.
4. What are the main environmental benefits of choosing a prefab building?
PEB buildings offer numerous environmental advantages. They significantly reduce construction waste compared to traditional methods, conserve resources through efficient design and material use, and are inherently more energy-efficient, lowering carbon footprints. The faster construction timelines also minimize disruption to the environment. Additionally, their adaptability and potential for relocation further reduce long-term impact.
5. Are PEB buildings durable and long-lasting?
Yes, PEB buildings are designed to be durable and long-lasting. They are built with high-quality materials and adhere to strict quality control standards in the factory. Additionally, the modular design allows for easy repairs and replacements, extending the building’s lifespan and minimizing the need for complete reconstruction.